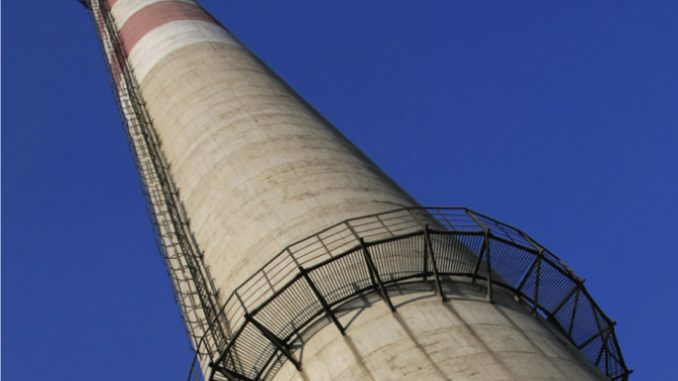
In a digital power plant, operations are monitored through over 10,000 sensor input points and the data drawn is interpreted to highlight the key factors (fuel quality, plant aging and ambient conditions) that at any point affect the performance of the plant. Besides, digital plants may seldom be equipped to take corrective measures regarding an anomaly in the operational performance in a closed-loop control system. Digitisation helps to ensure optimal operations of plants, improve performance, and enhance efficiency and reliability, while lowering the environmental impact.
Over the years, there has been a diversification in fuel-mix in the power generation segment, primarily with the large-scale penetration of renewable energy. Balancing the fuel-mix on a real-time basis is essential to maximise the energy output and cost-effectiveness of power generation in the country. In this regard, the digitisation of thermal power plants (TPPs) designed for uninterrupted operation is very essential as it helps regulate plant operations in an efficient manner.
Components of digital power plants
One of the critical aspects of a typical digital power plant is operations optimisation. It is carried out through applications that provide information on parameters, including efficiency, emissions and production costs, in response to any operational decision. Operations optimisation includes boiler optimisation, done through a software to improve boiler reliability and efficiency and reduce carbon dioxide and nitrogen oxide emissions by maintaining integrated enhancement of the combustion and soot cleaning processes; fuel analysers, which enhances the plant performance by tuning combustion and exhaust management processes based on fuel properties including moisture content; plant optimisation, done through a digital twin of the physical steam plant that is continuously monitored to identify gaps between the actual and ideal performance relative to key performance indicators such as output or emissions; monitoring load, which improves the load change performance, helping the operator to alter the power supplied to the grid on a real-time basis; and business optimisation, done through an application that aggregates information such as fuel and power price, demand and plant capacity, enabling energy traders to make better buying and selling decisions.
Another key component of a digital power plant is asset performance management, which is done through an application that continuously monitors plant equipment health, enabling operating teams to make decisions for enhancing plant performance, reduce unplanned downtime and extend plant life with minimal capital investment.
Key benefits of digital power plants
One of key benefits of digital power plants is minimising the environmental impact of TPPs. A digital power plant enables decarbonisation and ensures better plant economics, resulting in efficient fossil fuel usage. With digitisation of the plant, the operational performance can be monitored on a real-time basis and prompt action can be taken if emissions from a plant exceed the desired levels. Similarly, digitisation also helps improve the heat rate of plants.
The use of digital power helps maintain the health of the power plant machinery. The digital valves detect excessive wear and tear or process abnormalities that may lead to unplanned outages. It helps in the early detection and diagnosis of vibration and lubrication problems in a TPP. In addition, digital power plants offer integrated asset management through predictive intelligence that improves the capacity and availability at the plants. Digitisation allows the remote monitoring of operations by providing a secure view of plant processes. Self-diagnostics is yet another feature that minimises and helps avoid plant downtime.
Digitisation allows asset-level visibility of various power plant components. In order to obtain the desired operational result, it is essential to maintain a check on system operators in a real-time manner. The output of a TPP is linked to the state and performance of all assets linked to the network. Digitisation allows to continuously assess the demand and supply factors as expressed by all elements in a power system and respond to various price signals.
To conclude, digitisation of TPPs is the need of the hour for meeting the growing power demand in a reliable and cost-effective manner. It is a vital component for ensuring efficient and environmental friendly plant operations. However, in order to get the desired results, it is essential to analyse the data obtained through sophisticated software for deriving meaningful inferences, ensure data security against cyberthreats and provide adequate training to the workforce for operating digital power plants.