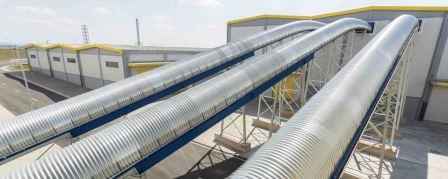
For long, industries such as cement, steel and sugar have followed a linear production model, under which a lot of waste heat generated during industrial processes goes unutilised. Given the quantum of waste heat energy available in these industries, several measures are being taken to utilise it such as cogeneration, waste heat recovery and more recently, trigeneration. These will help improve the overall energy efficiency of these industries, reduce their carbon emissions and achieve cost savings. A look at the different approaches and technologies being deployed by industries to improve their energy efficiency…
Key technologies
The average efficiency of conventional power plants is 35 per cent while the remaining 65 per cent of energy is lost. The major source of loss is the heat rejected during the conversion process to the surrounding water or air owing to limitations in the thermodynamic cycle of power generation. To overcome this inefficiency, a large number of industrial and commercial consumers are using cogeneration in their manufacturing process. As the name suggests, cogeneration is the simultaneous production of electricity and heat from a single fuel source such as natural gas, biomass, biogas, coal, waste heat, or oil. In a cogeneration plant, the low pressure steam from the turbine is not condensed to form water. Instead, owing to its high thermal energy, it is used for heating or cooling purposes in buildings and factories. The optimal design of a cogeneration plant increases the overall efficiency to 85-90 per cent, which is much higher in comparison to conventional power plant efficiency. Apart from the efficient use of fuels, cogeneration helps reduce greenhouse gas emissions. Further, as the production of electricity is mostly on-site/captive, the burden on the utility is reduced and losses due to transmission and distribution are mitigated. Cogeneration plants are being used by a number of energy-intensive industries in India such as sugar, textile, chemical and pharmaceutical, paper and pulp, refineries and fertiliser. A number of sugar mills use their own bagasse to run their mills during the crop season and generate steam to run the boilers and turbines. They export the surplus energy to distribution licensees.
A sister technology of cogeneration is waste heat recovery, which involves capturing waste heat discarded by an industrial process and using that heat for other applications such as electricity generation. Considering the latest advancements in waste heat recovery systems (WHRS) in the past decade, it has become possible to harness power from the low/medium temperature heat range that is, through organic Rankine cycle, or Kalian cycle, etc.
In India, a major application of the technology is in the cement and steel industries. In the cement industry, waste heat from cement kilns is used for drying of raw materials and fuels. Owing to moisture in the raw materials and the use of cooler technology, additional waste heat is extracted from the kiln gases and cooler exhaust air, which is then used for electricity production. This helps in increasing the energy productivity, thus reducing the operating costs for facilities. Besides, WHRS helps save fossil fuels such as diesel, high grade coal and furnace oil. Many industrial units such as Reliance Industries Limited, Monnet Ispat and Energy Limited, and Gujarat Alkalies and Chemicals Limited have installed WHRSs at their factories for captive use. Further, given the ban on pet-coke, more companies, particularly in the steel and cement industries, are realising the importance of heat recovery and are effectively utilising it. The installation of WHRSs at captive generation plants can meet 20-40 per cent of power consumption requirement for a given industry. Another extension of the same concept that helps in the reduction of waste heat energy is trigeneration. Trigeneration is the combined process of cooling, and electricity and heat production. The gas-fired generator produces electricity and heat while the exhaust heat goes to the absorption chiller, which produces chilled water and hot water for air conditioning.
Trigeneration plants are mostly installed at those locations that can benefit from all three forms of energy such as hospitals, airports, hotels and shopping malls. Both cogeneration and trigeneration can significantly bring down energy costs and improve energy efficiency. According to Energy Efficiency Services Limited, trigeneration has a potential of over 20,000 MW in India across industries. Also, as per recent audits of potential trigeneration projects, their payback period is as short as two to three years. Further, trigeneration plants allow up to 80 per cent of primary energy to reach end use, as opposed to only 25 per cent in conventional power plants.
However, according to industry experts, the success of trigeneration systems relies on regular, affordable gas supply. Therefore, a favourable regulatory environment is required for gas distribution and pricing. Trigeneration can be even more profitable and environmentally sustainable using low-cost “opportunity fuels” such as methane from agricultural or food processing wastes, landfills, or wastewater treatment plant digesters.
Other energy efficiency approaches
Industries are adopting other approaches to improve power plant efficiency. One of the options for improving the overall performance of a gas turbine power plant is to modify key turbine components in order to allow an increase in the firing temperature.
This modernisation helps increase the power output, improve heat rate and generate additional exhaust energy. Other approaches for improved gas turbine and system efficiency are use of improved materials with better high temperature capability and improved cooling techniques (film cooling in the first rows of blades and vanes), development of thermal barrier coatings, use of variable speed drivers in process control (for reduction in the auxiliary internal consumption) and advancements in the aerodynamic design for blades. Meanwhile, a number of commercial and industrial units have shifted towards renewable energy based power plants to fulfil their power requirements while reducing their overall carbon footprint. The shift towards renewables can also be attributed to the declining wind and solar energy tariffs and the incentives provided to industrial consumers for the use of such sources.
Moreover, industries have been focusing on replacing conventional fuel in their manufacturing facilities. In the cement industry, energy costs and environmental concerns have encouraged companies to evaluate the extent to which conventional fuels can be replaced by waste materials. A variety of industrial by-products are now being used as alternative raw materials/fuel in cement kilns. These include hazardous waste, refuse-derived fuel from municipal solid waste, used tyres, biomass and industrial plastic waste. The use of alternative fuels also helps in the sustainable disposal of industrial and agricultural waste. New types of cements have been introduced such as geocement, microfibre cement and limestone calcined clay cement. Such innovations also drive a significant reduction in the industry’s overall carbon dioxide emissions.
Conclusion
Industries have a huge potential for improving their energy efficiency through energy efficient technologies and renewable energy options. While these innovations offer economic and environmental benefits, there are financial constraints with respect to the adoption of the technologies. Moreover, companies need to invest in research and development, and take appropriate technological measures as per the plant requirements. Many industries are still using obsolete technologies for their processes. Therefore, the need of the hour is to scale up the energy efficiency programme in order to achieve substantial gains at an aggregate level.
With inputs from presentations by A.K. Sinha, General Manager-CPP, BHEL, and Vivek Taneja, Director, Business Development, Thermax India Limited, at a recent Power Line conference